Are you looking for a
TRUE MODULAR SOLUTION?
100% CUSTOM DESIGN WITH USP797 & USP800 COMPLIANT
CLEANROOM LOGIC is the specialized company for designing modular & structural cleanroom. CLEANROOM LOGIC is the best supplier who serves the best quality and best price for every customer of the domestic and overseas markets. An inquiry or request from any potential customers are always welcome.
Cleanroom Logic have over 10 years experance with many satisfied customers world wide and we are constantly working hard to improve by each project.
What is Cleanroom
A cleanroom or clean room is a facility ordinarily utilized as a part of specialized industrial production or scientific research, including the manufacture of pharmaceutical items and microprocessors. Cleanrooms are designed to maintain extremely low levels of particulates, such as dust, airborne organisms, or vaporized particles. Cleanrooms typically have a cleanliness level quantified by the number of particles per cubic meter at a predetermined molecule measure. The ambient outdoor air in a typical urban area contains 35,000,000 particles for each cubic meter in the size range 0.5 ?m and bigger in measurement, equivalent to an ISO 9 cleanroom, while by comparison an ISO 1 cleanroom permits no particles in that size range and just 12 particles for each cubic meter of 0.3 micron and smaller.
Cleanrooms maintain particulate-free air through the use of either HEPA or ULPA filters employing laminar or turbulent air flow principles. Laminar, or unidirectional, air flow systems direct filtered air downward or in horizontal direction in a constant stream towards filters located on walls near the cleanroom floor or through raised perforated floor panels to be recirculated. Laminar air flow systems are typically employed across 80% of a cleanroom ceiling to maintain constant air processing. Stainless steel or other non-shedding materials are used to construct laminar air flow filters and hoods to prevent excess particles entering the air. Turbulent, or non-unidirectional, air flow uses both laminar air flow hoods and nonspecific velocity filters to keep air in a cleanroom in constant motion, although not all in the same direction. The rough air seeks to trap particles that may be in the air and drive them towards the floor, where they enter filters and leave the cleanroom environment. US FDA and EU have laid down guidelines and limit for microbial contamination which is very stringent to ensure freedom from microbial contamination in pharmaceutical products.
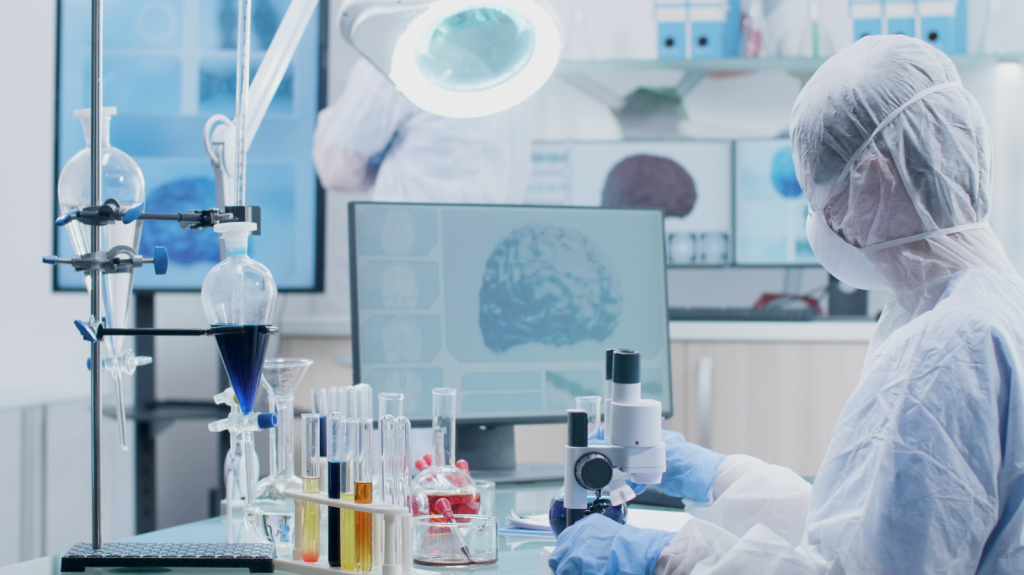
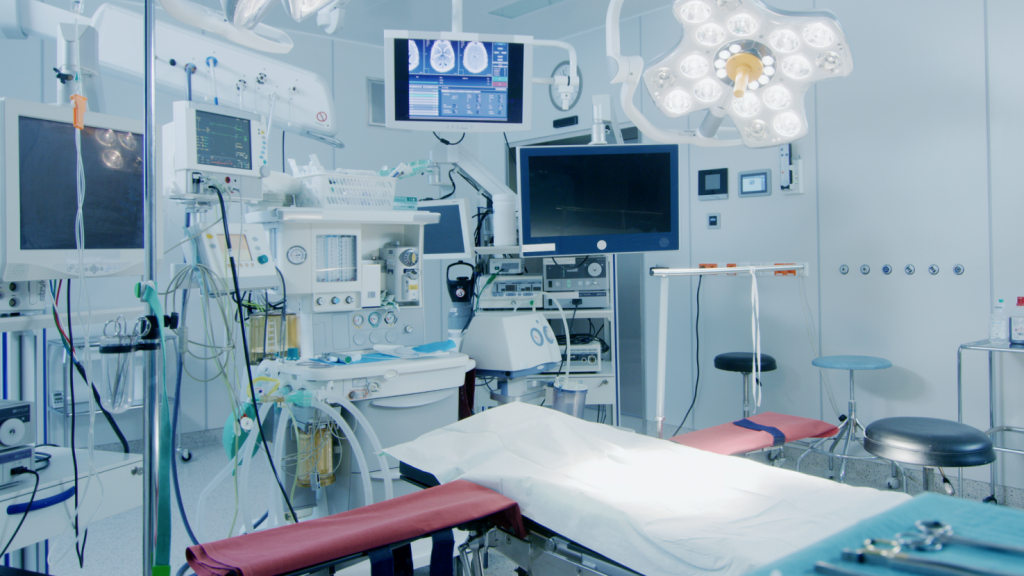
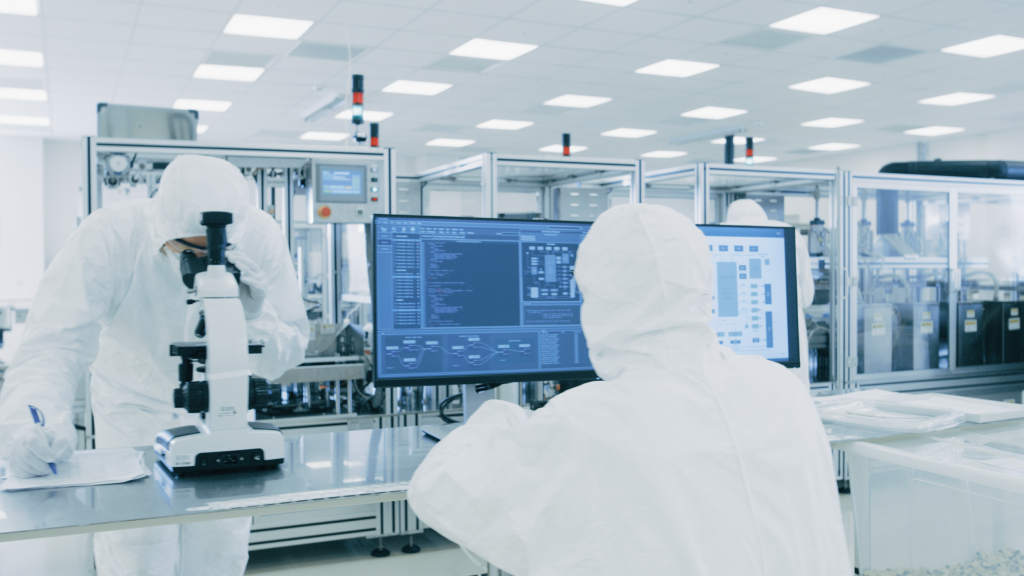
Modular vs Structural?
One of the most significant differences in these building methods is time. Since modular construction can be done simultaneously in a factory and on-site, it can be completed up to 50% faster than traditional construction. This is especially appealing for commercial use since business owners begin to see a return on investment much sooner than with stick-built construction.
How can a building be built to last in such a short amount of time? Steps to ensure efficiency, durability, and dependability are the top priorities in modular builds, just as they are in traditional construction builds.
If you still have doubts regarding the process of modular vs. traditional construction, refer to this infographic that outlines the main differences between the two processes. The advantages of modular are evident when viewed through a side-by-side comparison.
Why Modular Cleanroom?
Modular is demountable and 100% re-usable Modular is mobile and can be relocated anytime IRS treats modular walls as furniture Modular is not a permanent structure. Under the Modified Accelerated Cost Recovery System (MACRS), modular walls are classified as “tangible property” with a 7-year depreciable life. (the Section 179 Deduction) *consult with your tax preparer
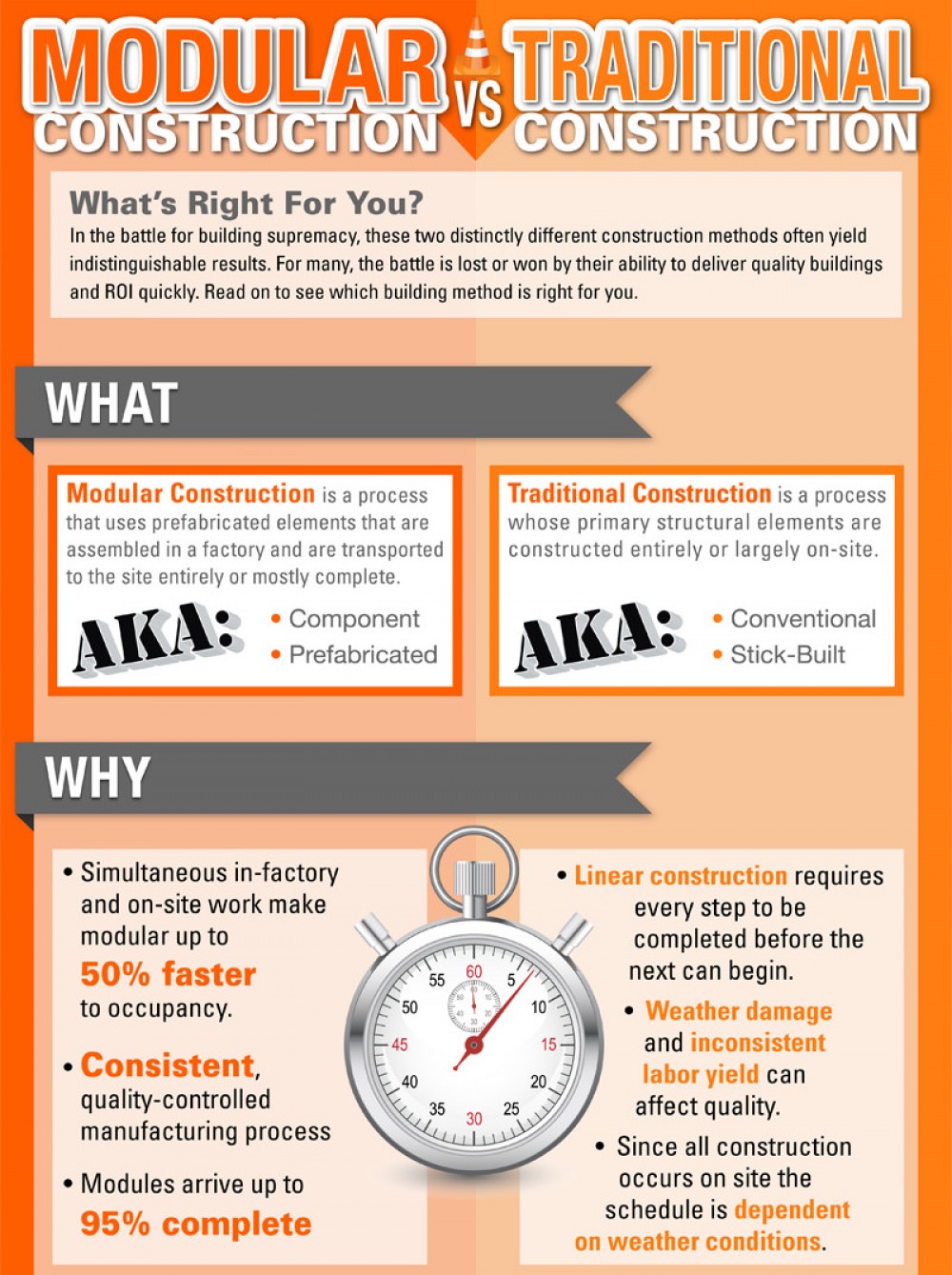
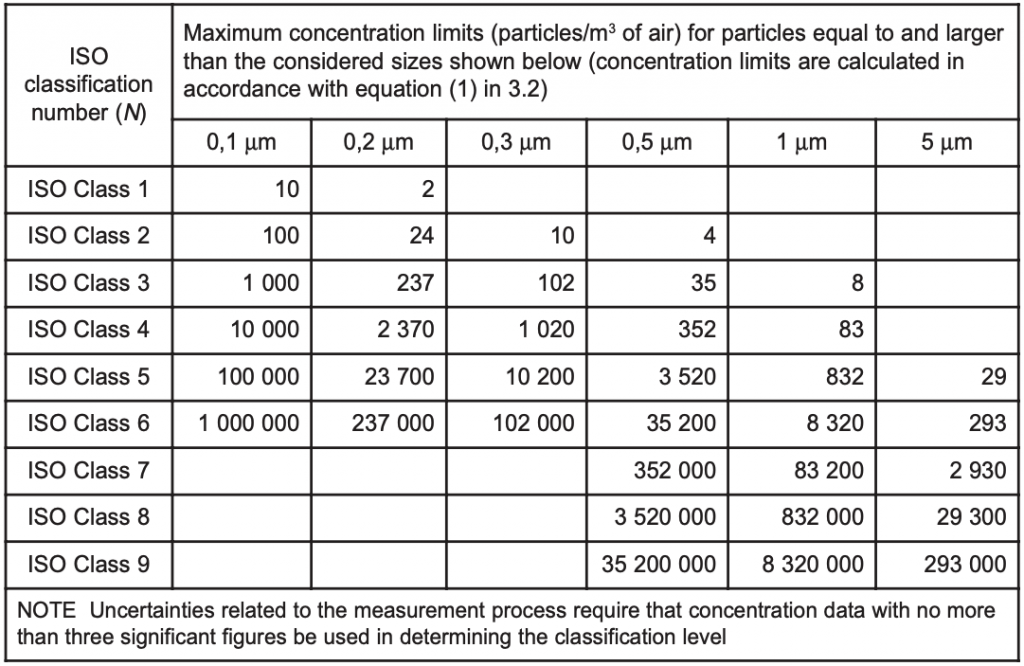
Modular Cleanrooms Applications
- USP-797 Sterile Compounding Pharmacies
- USP-800 Non-Sterile Compounding Pharmacies
- Medical Device Production & Packaging
- Laboratories
- Life Science Industry
- Wafer Fab Production
- Optic Assembly and Packaging
- Nano Technology
- Pharmaceutical Industry
- Controlled Environments
- Clean Manufacturing
- CMM Rooms
- Cannabis Process and Manufacturing
ISO Class Average number of air changes per hour
ISO 5 240–360 air changes per hour (unidirectional airflow)
ISO 6 90–180 air changes per hour
ISO 7 30–60 air changes per hour
ISO 8 10–25 air changes per hour
Conventional building 2–4 air changes per hour